“Steel or concrete?” This has been the standard question on commercial projects for generations. But the industry is changing—mass timber is quickly becoming a viable and exciting third option for high-rise and high-occupancy commercial and multifamily buildings.
For years, builders could only erect wood structures to five stories and 65 feet of wood. However, new legislation in Washington and Oregon allows this renewable material for hybrid buildings up to 270 feet tall, using a combination of engineered mass timber (MT) products (most notably cross-laminated timber, or CLT) and structural steel or concrete lateral systems.
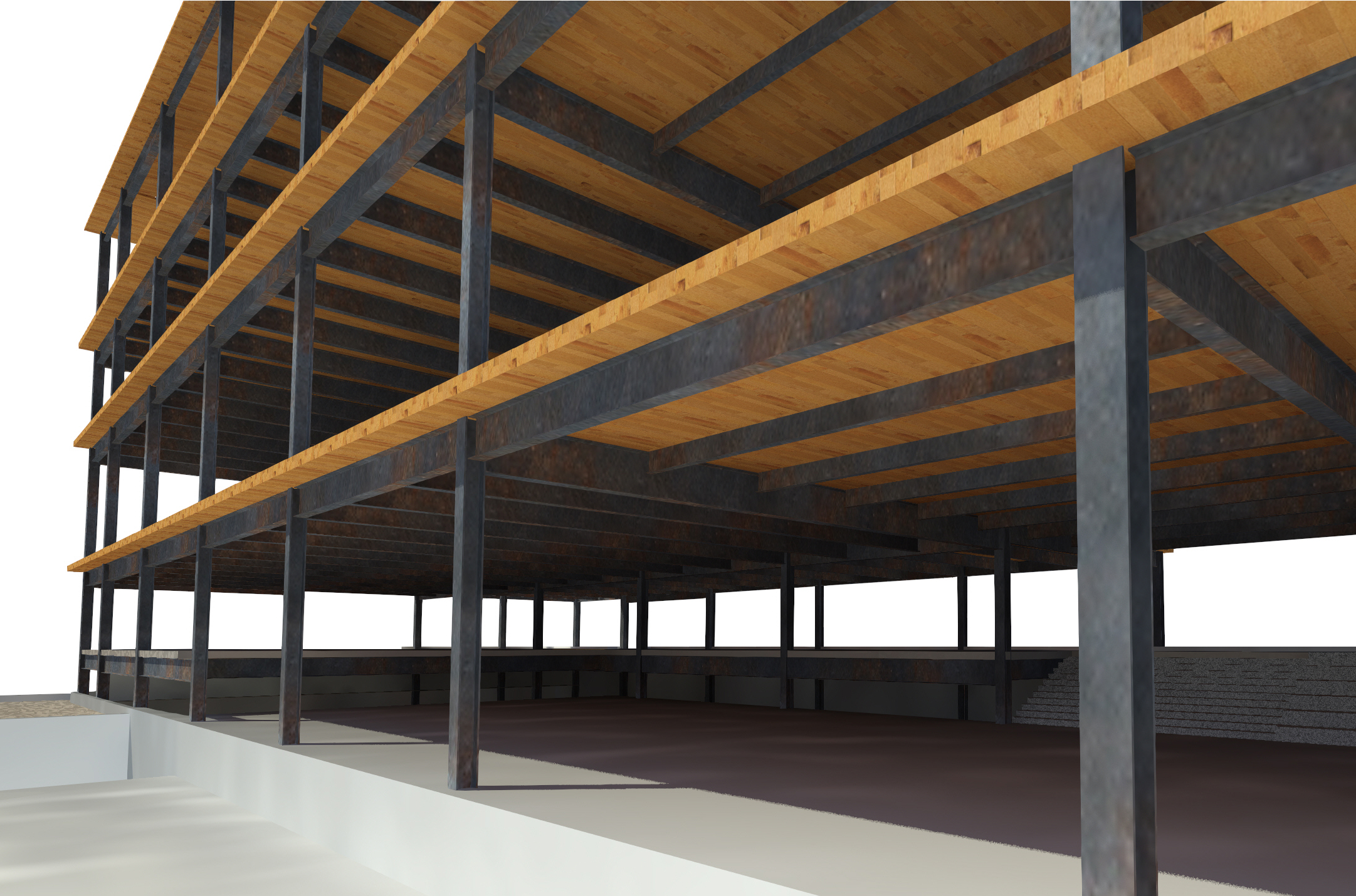
Many of our clients are excited about mass timber’s sustainability, aesthetics and occupant-health benefits, but ask an essential question: “What does it mean to my budget and schedule?”
The short answer is that cost remains a hurdle in most cases. Currently, mass timber is attractive for projects where aesthetics and sustainability are worth an added investment. But we expect costs to fall relative to other structural types. (Some say costs can be similar already, such as a study group with DLR.)
Schedule is already an advantage. Mass timber is often modularized into large components, which can shorten onsite construction durations by months, with some added manufacturing lead times.
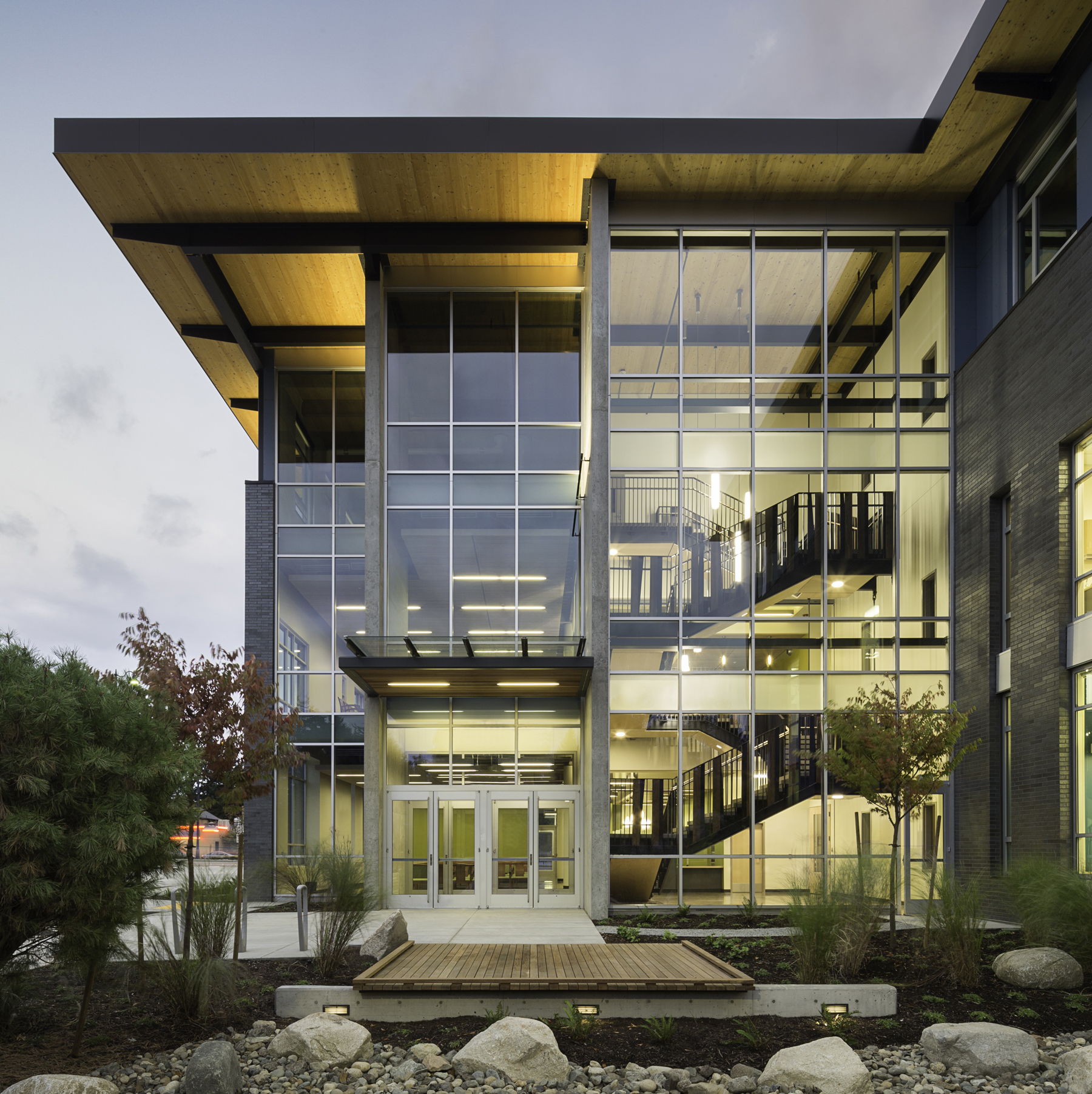
We see several cost and schedule trends that should be considered when planning a mass timber project—most pointing toward increasing viability:
- The supply chain is maturing. The market is strong for simple pieces on small buildings, but limited in terms of larger manufacturers capable of producing 40-foot or longer mass timber panels, or supporting the schedules needed for larger buildings. We hope to see more fabricators and expanded production capacities in the near future. Added competition and the capability of producing larger panels will open greater possibilities for design.
Progress is encouraging, including Katerra’s new plant in Spokane which can accommodate panels up to 60 feet long and Vaagen Timbers’ new plant in Colville.
- Builders are learning. The more we know, the more efficient and predictable projects become. Over time, contractors will develop more historical pricing, build stronger relationships with a wider array of fabricators, use VDC more effectively to coordinate integral systems and connections and more easily find schedule and savings opportunities.
Jacob McCann, Principal at KPFF, shared his thoughts. “It will be helpful to improve benchmark cost and schedule information as more MT/CLT projects are designed and constructed,” he said.
- Engineering is becoming streamlined over time. Our industry already enjoys prescriptive design efficiencies and straightforward codes for mass timber’s gravity performance, but codes for mass timber shear walls have yet to be updated based on full-scale earthquake testing. Currently, engineers need to either apply conservative prescriptive load factors that result in conservative (and often expensive) designs or run time-consuming non-linear analyses. With much of the testing and review now complete, the American Society of Civil Engineers will develop more accurate, less conservative parameters soon.
“This will eliminate the need for project specific testing, which is usually not feasible due to cost and schedule constraints. It will also add certainty to the timeline for permit approvals,” McCann said. He added “CLT floor designs will gain efficiency as analysis procedures are developed for floor vibration.”
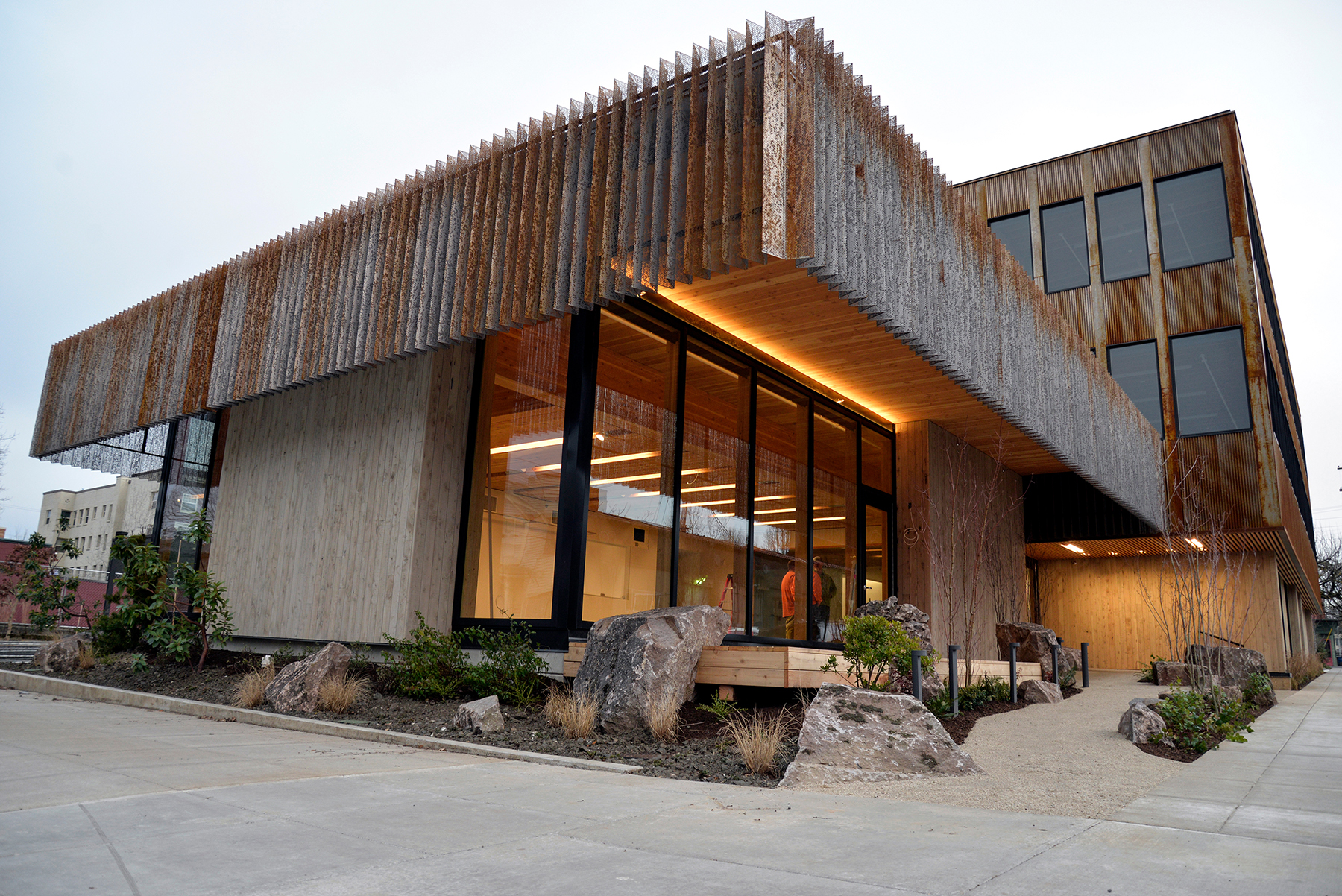
- Modularization is gaining popularity. Factory assemblies can allow major structural and wall components to fit together quickly onsite. This is a major schedule advantage with potential to save cost. Suppliers have begun to bring other trades into these assemblies, including mechanical and electrical systems as well as metal elements of composite structural systems.
A good builder will seamlessly integrate these systems with VDC prior to fabrication. As with any modularization, prefabricated mass timber panels can reduce onsite durations but require earlier coordination of all systems involved.
- Products will advance and gain economies of scale. Ideally, non-proprietary fasteners and other connection hardware will mass produced, ensuring more competition and lower costs. The industry is seeing progress in mass production, with some risk of proprietary systems that leave projects bound to single suppliers. As a general contractor, our job is to help identify risks related to single-source providers and work to mitigate those through subcontract language and back-up plans.
It’s important to note that use of mass timber can avoid other costs. For example, it can eliminate the need for gypsum wall board for fire protection when the building falls in certain code categories, and can reduce the need for other interior finishes. At the same time, exposing systems can mean spending more for aesthetically pleasing mechanical and structural details. Your general contractor and subcontractors can help identify opportunities and challenges early in design.
Mass timber appears to be close to broad viability for large-scale commercial and multifamily construction. Market efficiencies, prescriptive design and ever-smarter team analysis will continue to drive costs and schedules down. Yesterday’s niche concept might become a “must consider” option for your projects in the near future.
Part 2 will discuss details of how Lewis is making mass timber successful on our projects.
Scott Akre, Senior Preconstruction Manager at Lewis, has studied or built mass timber projects for multiple clients including the UW and ICHS. Kate Pfretzschner, PE, is a project engineer at Lewis and earned a master’s degree in Structural Engineering and Wood Science.