In part one of this series, we gave an overview of Rainier Square’s structural core: a series of prefabricated sandwich modules, hoisted into the sky, set in place between columns, welded, and filled with concrete. Simple, right?
On paper, yes. Put a piece in place, weld it, then fill it. But that skips all the “how are we…?” questions. How are we going to get the modules from the Supreme Group to the build site? How are we going to lift them? How are we going to fill them?
In order to answer these questions, Lewis formed an integrated team with MKA, The Erection Company and Supreme Steel to work through the details of construction. The keys to successful implementation of the concept were two core mockups the team assembled prior to breaking ground. The mockups provided solutions to some perplexing problems that would have derailed the project if they had gone unsolved.
Transport
To get to their final resting place, each piece of Rainier Square steel took a 174-mile truck ride from The Supreme Group’s yard in Portland to Rainier Square in the busy downtown Seattle core, followed by a several-hundred-foot flight through the air via a crane. The thing is, these modules were designed to sit vertically in a building core, not flat on a truck traveling up I-5 or swinging through the air from a crane.
The team was faced with a litany of questions: How can we eliminate damage to the modules while on the truck ride? Is it safe for the interstate? How can we safely lift it via the crane? As it’s being tilted from a horizontal to a vertical position, will the module experience any detrimental flexing? These modules were big, heavy and precision engineered to fit with the neighboring steel, so the entire trip from steelyard to building core needed to be safe and predictable.
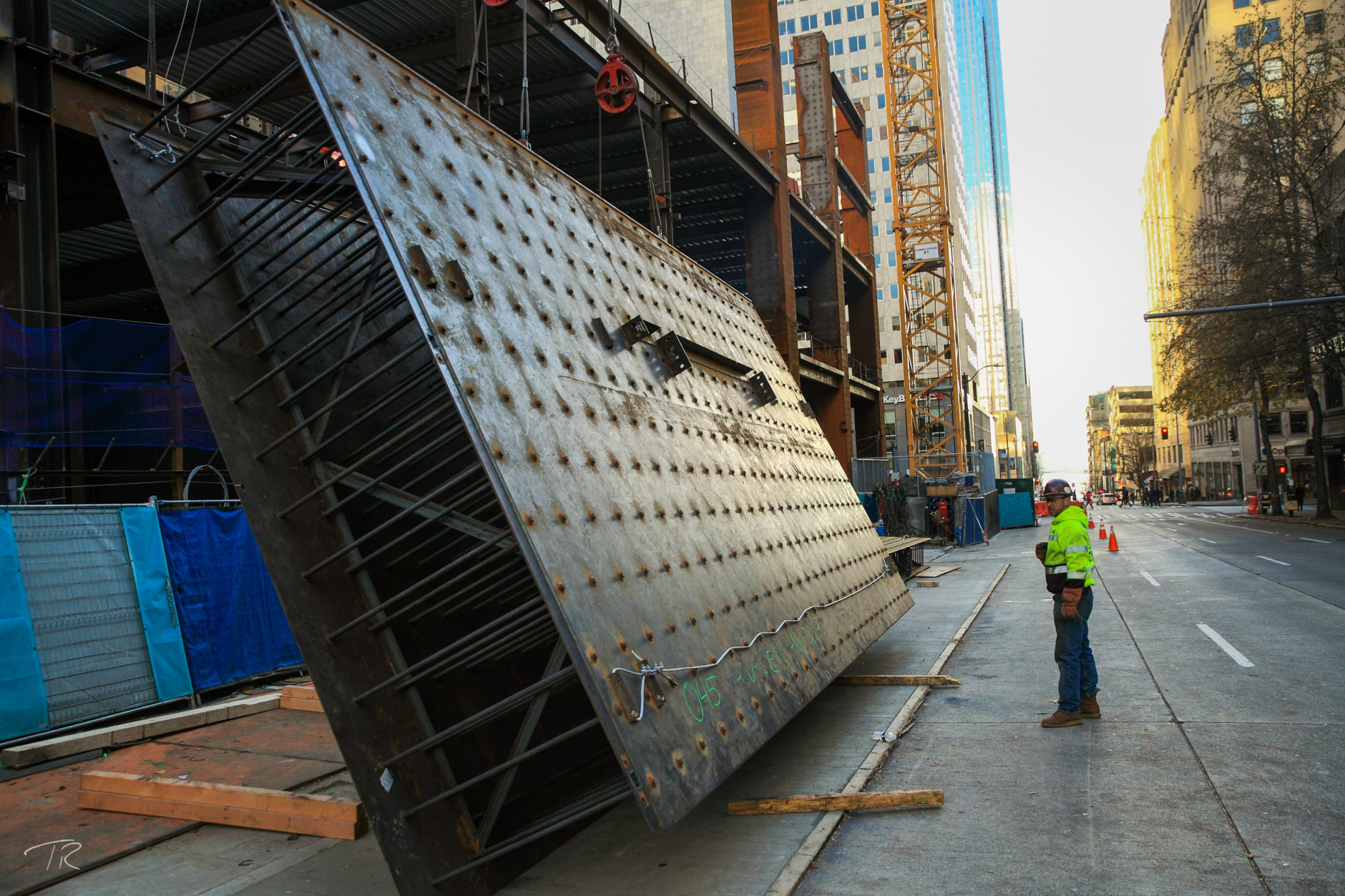
Concrete
A critical aspect of this core system is the concrete fill between the plates. In order to provide the necessary structural integrity, the concrete needs to evenly fill the entire module, flowing into each crevice and corner. During concrete pours for columns or walls in a typical structure, concrete is either poured from the top—the most convenient approach—or pumped in from the bottom up, a method which prevents voids from forming in the fill.
However, Rainier’s core presented several issues:
- Steelworkers would be placing new modules above while concrete was being poured into the ones already placed, so an overhead approach was out of the question.
- Pumping concrete from the bottom of each module would work—until the core reached a certain height. At this point, the power of the street-level concrete pump would not be able to overcome the downward force of the concrete in hundreds of feet of vertical hose.
- A typical concrete mix—consisting of sand and aggregate—wouldn’t flow and consolidate properly through the connecting rods, around the doorways and into the corners of the core wall modules.
Welding
A second key to the structure is the numerous welds throughout the core. Each module is welded along its seams to adjacent columns by a steelworker with typical welding equipment. The core’s numerous inside angles and precision fit made accessing the welding locations extremely challenging, so the team had to figure out how to get a steelworker and all their equipment into the right place at the right time…for 58 levels. Safety was paramount, as was simplicity and repeatability.
The Solution: Mockups
The Rainier Square team was faced with challenging problems, which, if they went unsolved, could prevent the tower from being a success. Poring over 3D models, sketches and diagrams only took the team so far: they knew their best chance of success was to actually build it.
So, that’s what the team did: two full-scale mockups.
The first mockup was a full-scale plywood, proof-of-concept model. This effort tested a new concrete mix specially made for this core. Stripping away the plywood forms of this mockup allowed Lewis to confirm that this unique, aggregate-free concrete mix developed by Lewis and Stoneway Concrete would flow into all the nooks and crannies of the core, thereby ensuring the structural integrity of the core.
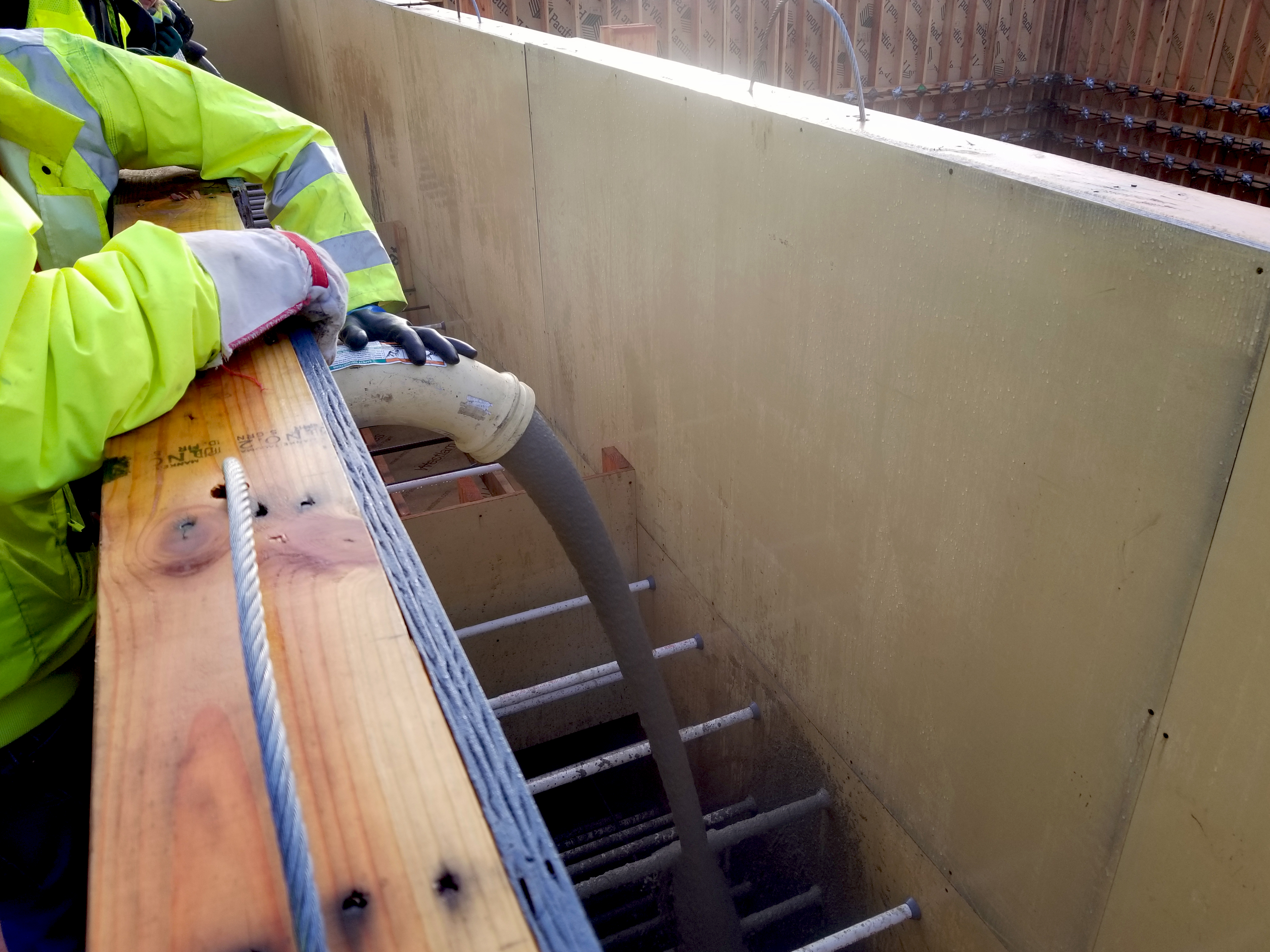
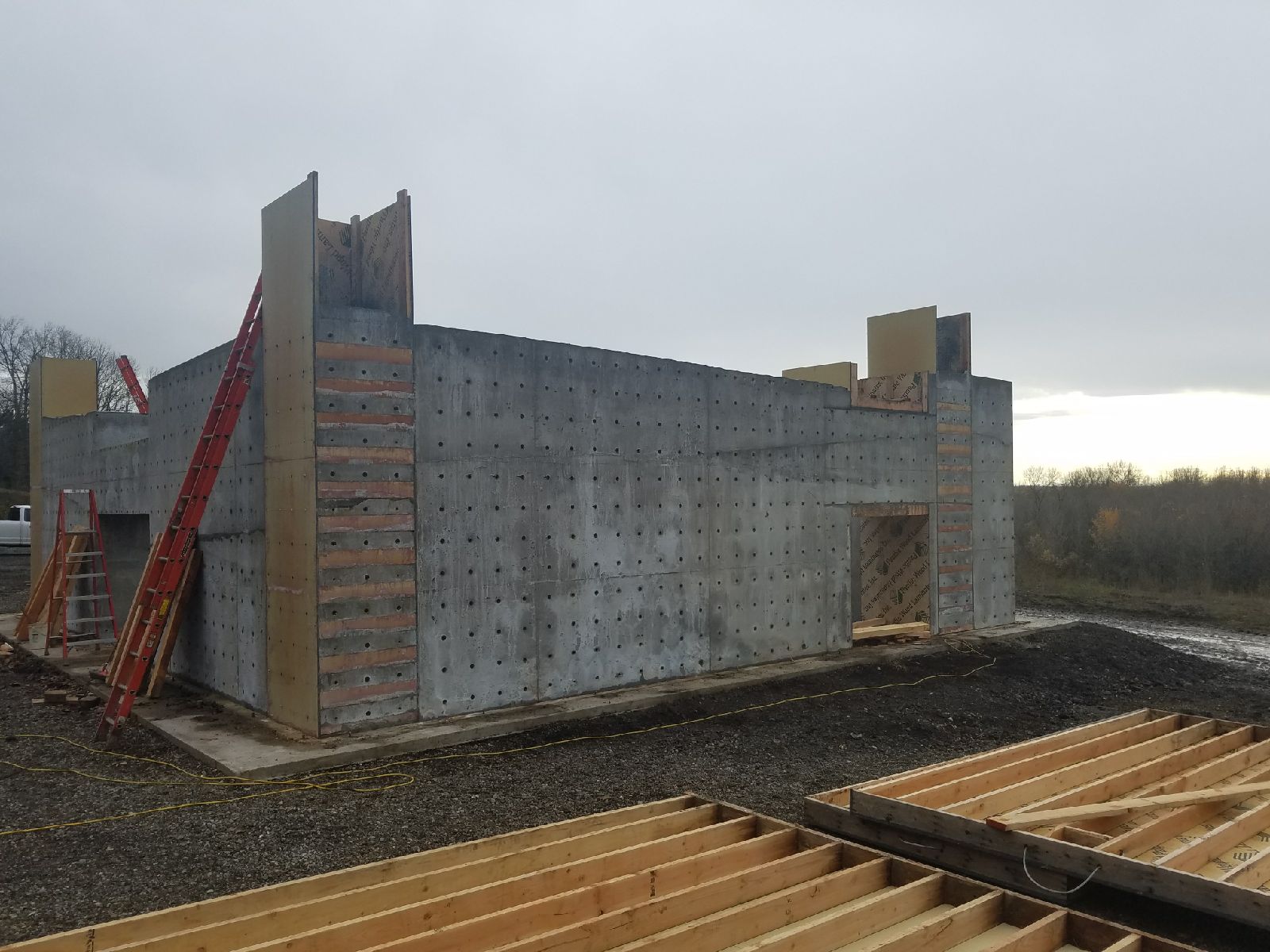
At the same time, it uncovered some issues related to where the concrete was actually poured into the forms and how it consolidated. Overall, the first effort accomplished what it needed to do: prove that the idea of a concrete-filled core could work.
The second mockup took all the lessons learned from the first and applied them to a full-scale, all-steel version. This effort resulted in several confirmations and refinements to the core wall modules, as well as a better understanding of site logistics.
- New locations for concrete portals: the team found out that pouring in from the corner columns—each of which had to be perforated with a very specific pattern of portals to allow the concrete to flow properly—resulted in perfect consolidation.
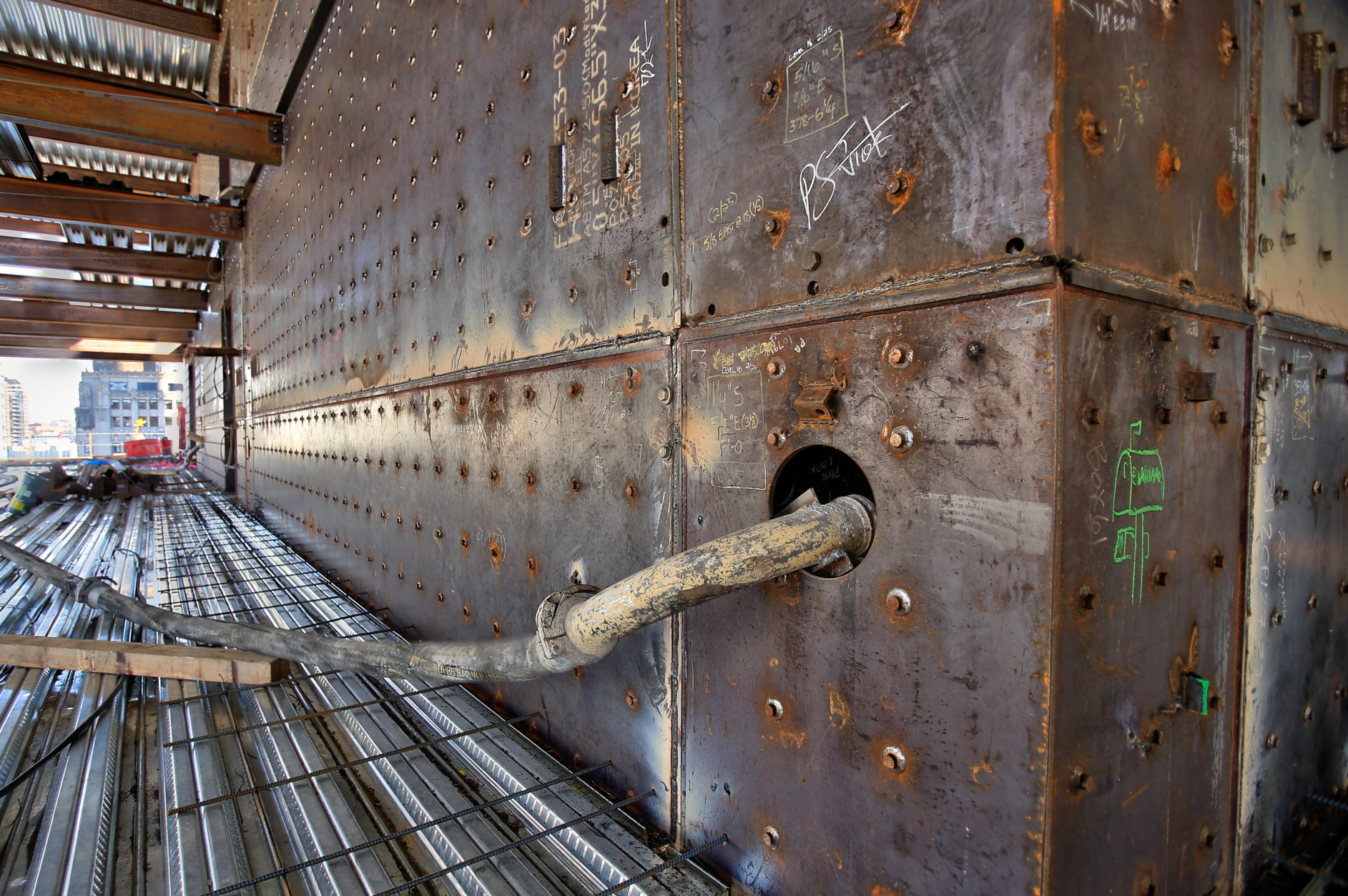
- Welding access points: since each module needs to be field-welded to the adjacent modules and columns, access for welders is critical. During this mockup, the team added several welding access points for crews to work through.
- Durability, rigging, and sequencing: before beginning its life as a piece of the Rainier Square puzzle, each module had to be transported from Portland, Oregon, staged on the jobsite and flown into place. This required extra steel supports through the center of the modules, crane lift points and a dry-run of the assembly of one floor’s worth of modules.
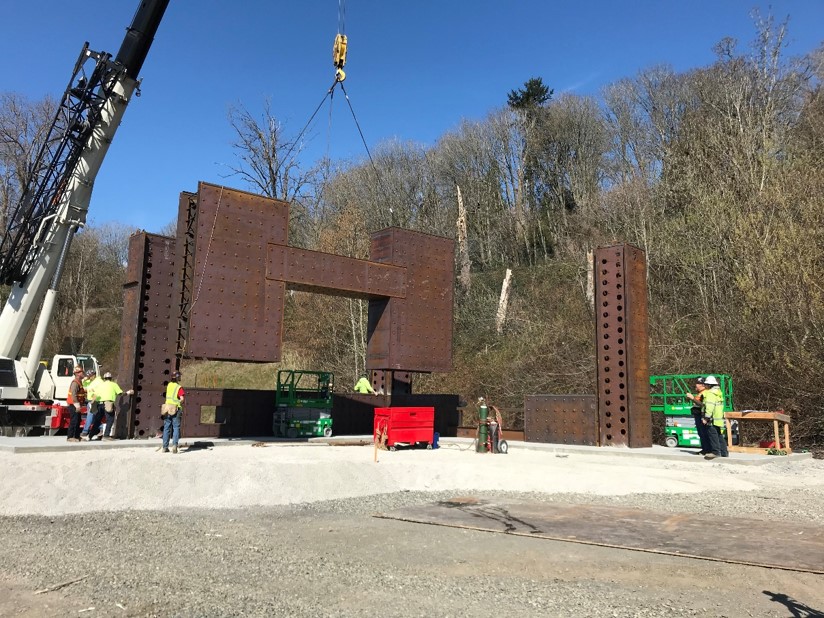
Overall, these mockups not only confirmed that Rainier Square could be built, but how it would be built. They taught the team how to move, lift, weld and fill the modules. Once these mockups were shown to be a success, it was finally time to start building.
Fast forward to today, just 10 months after starting to build Rainier Square: the tower has successfully topped out, achieving the goals of the whole project team. Rainier Square’s innovative structure is no longer a just a theoretical concept….it’s now a proven method of construction.
Now, the only question is, what’s next? What do we do with this newly acquired knowledge? That’s a big question, and we’ll explore it in the final installment of this three-part series.