In November 2023, University of Washington Bothell and Cascadia College celebrated the opening of Innovation Hall, a shared academic building that allows for the significant expansion in STEM research and education in Washington state.
The project is the first academic building in the nation shared by a community college and a university. Using a progressive design-build delivery, the wider project team, led by Lease Crutcher Lewis and design firm Mithun, leaned on its collective knowledge and resources to navigate unexpected hurdles along the way.
The $79 million, 80,000-square-foot Innovation Hall offers programs including biology, chemistry, computer science, physics and electrical and mechanical engineering, with classes open to both institutions.
A unique teaming approach
For the first time in Washington state and for design-build projects administered by the University of Washington, both UW Bothell and Cascadia College selected the project’s design-builder, Lewis, before the rest of the team was formed.
Lewis then chose the architect, Mithun, with input from UW’s Architectural Commission, UW Bothell, and Cascadia College. Afterward, Lewis and Mithun built out the design-build team roster with preferred consultants and trade partners.
The UW has since used this new approach to lead team selections for several large projects.
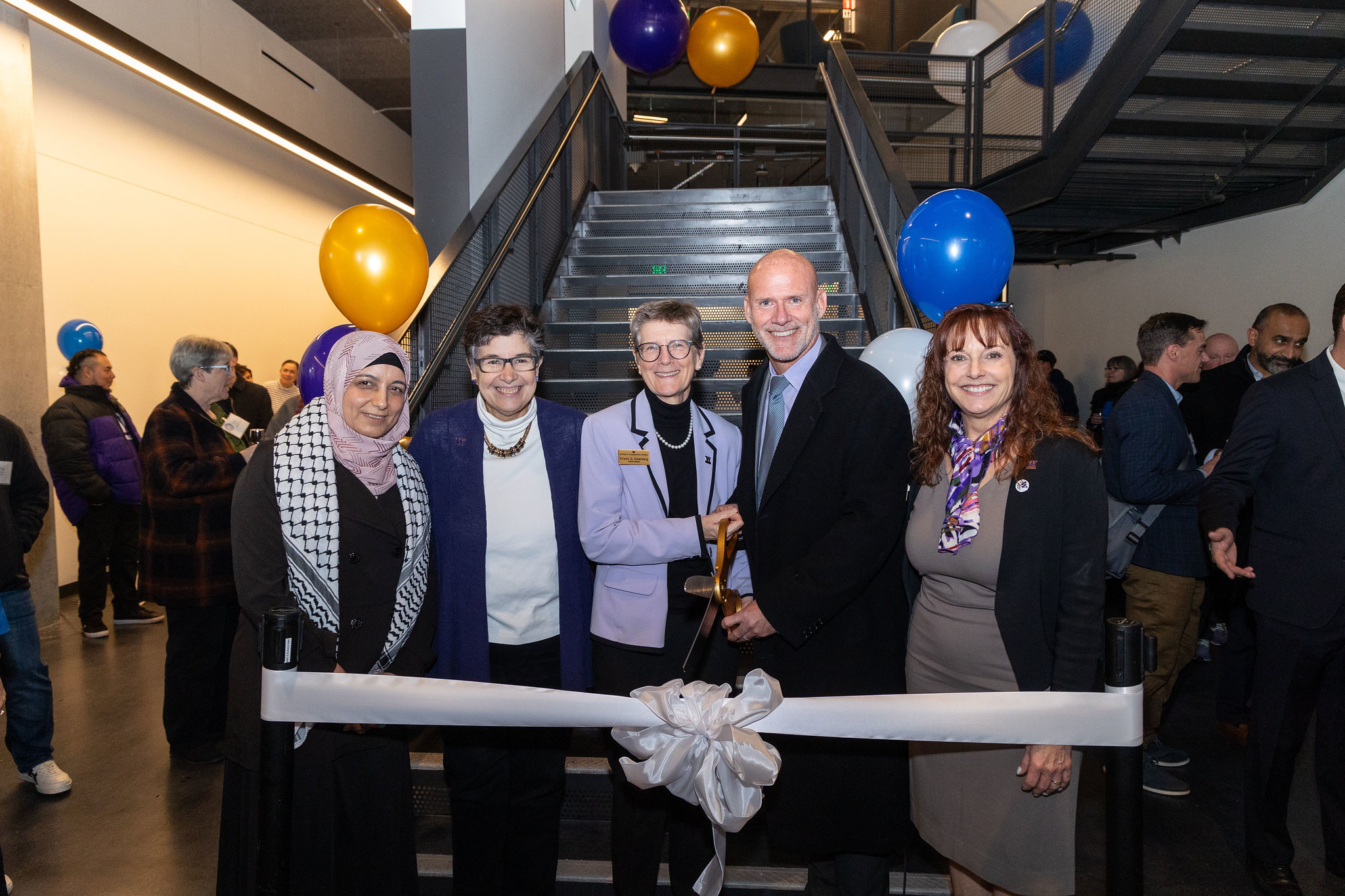
More space for the money
Initially, the design-build team presented the institutions with several base programs and footprint configurations to choose from, each for the same fixed budget. Because the owners prioritized oversizing the building (relative to existing benchmarks) and having the most instructional space possible, the team sized the project at 80,000 square feet.
This meant that some of the interior buildouts had to be excluded from the base budget and would rely on the availability of contingency funding set aside by the project team. The institutions and the design-build team called this stretch goal “overbooking the flight.” If traditional waste could be reduced from the process and the risks mitigated, those funds could be redeployed toward building out the shell space.
This incentivized everyone to work toward a common goal, manage the risks collectively, and get a proportional reward. By forming the team early and through thoughtful risk management, the project team weathered a variety of unforeseen challenges while maintaining enough contingency funding for the larger building.
Ultimately, this included 12,000 square feet of interior buildouts that may not have otherwise been completed, plus improvements like access controls, audio-video upgrades, all-gender bathrooms, and added lab exhaust capacity.
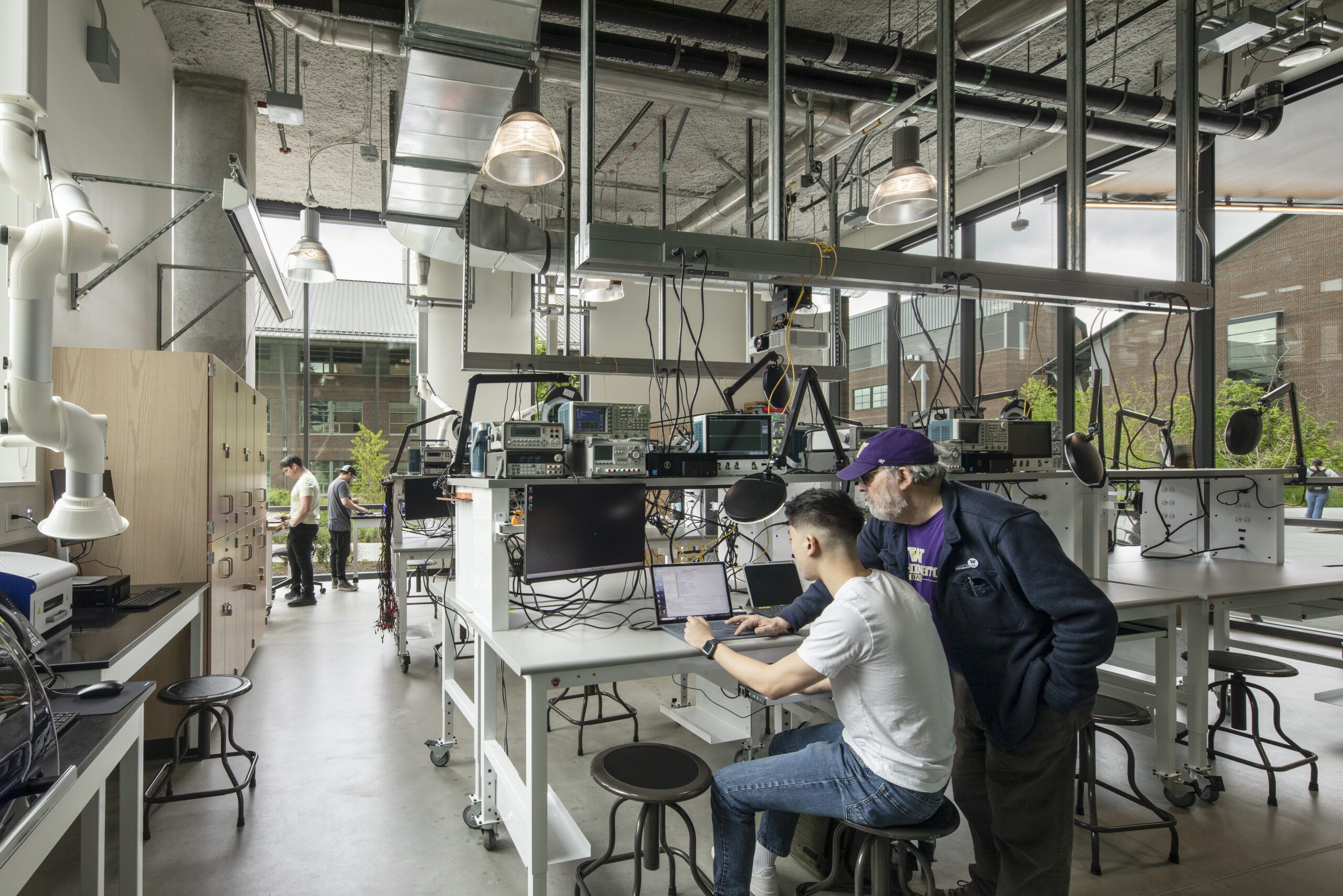
The building is 12 percent larger than comparably-priced academic buildings, allowing for more instructional space—more labs, more classrooms, and more collaboration and faculty space for both institutions—and while serving an additional 72 full-time students each year.
Weathering major work stoppages
In late 2021, hundreds of concrete mixer truck drivers went on strike, halting projects across the Puget Sound region. The nearly five-month stoppage came at one of the most inopportune times: when Innovation Hall’s concrete structure was the project’s critical path.
On the first morning of the strike, trucks were scheduled to arrive at 8 a.m. but didn’t show. Concrete footings had just been placed and the team had just erected vertical sheer walls and column forms.
The empty column forms and wall forms stood empty for 145 days, as did the project’s elevator pit, which was scheduled for a cement pour on the day the strike began.
The concrete drivers’ strike delayed Innovation Hall by four and a half months, ultimately costing the project team 54 percent of its available contingency funds. With its thoughtful approach to risk management, the team was able to absorb the costs without asking the owners for more budget.
This strike followed an early carpenters’ strike in September of 2021, which resulted in a few weeks of lost work.
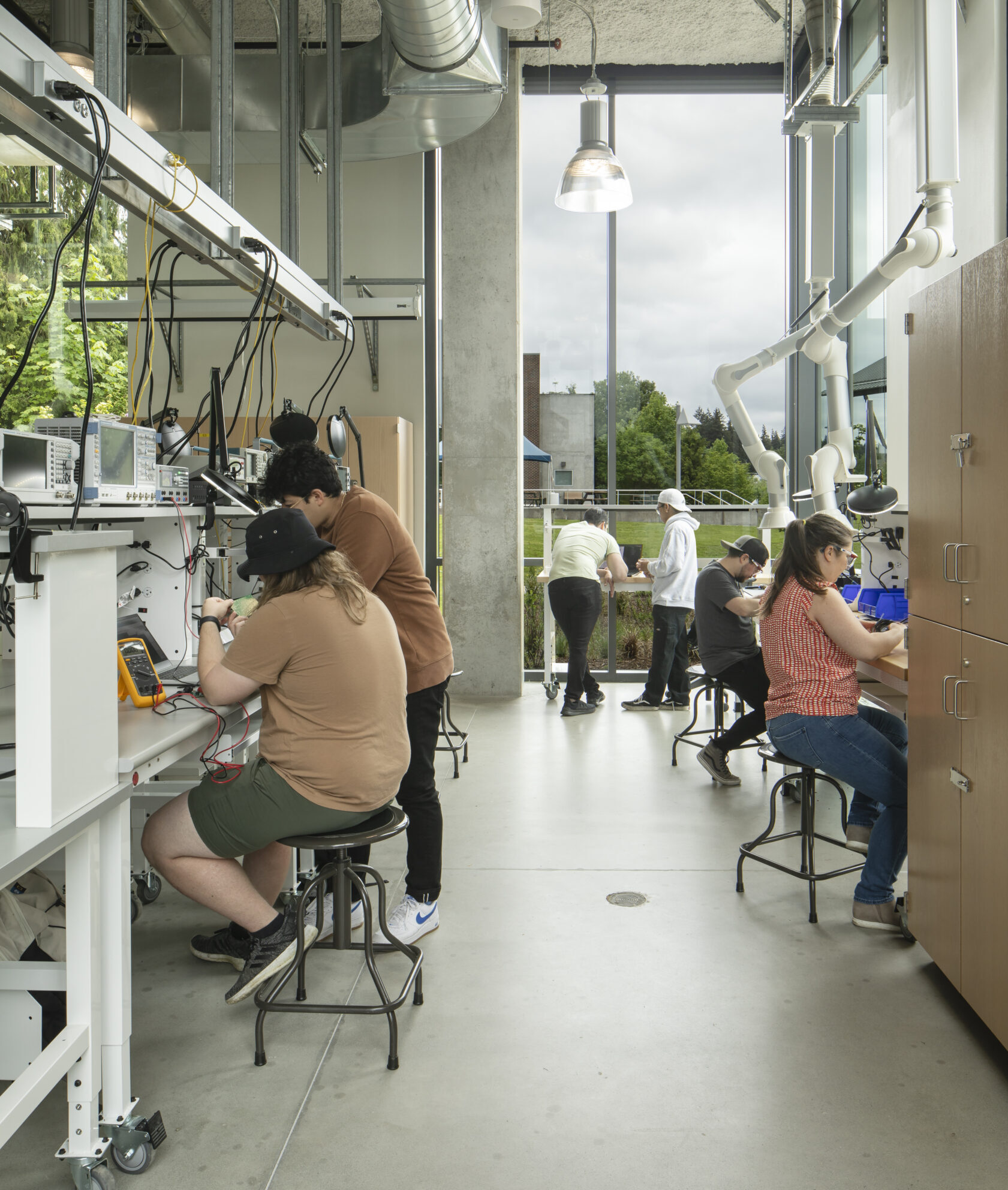
Navigating pandemic-related challenges and uncertainties
The project team faced significant cost escalations during the pandemic, with the cost of materials, equipment, and building systems skyrocketing and requiring unprecedented lead times. When it came to formwork, for instance, the cost of plywood had increased nearly ten-fold. Some equipment and building systems took a year and a half to arrive on-site.
Early engagement with selected trade partners helped with the design, detailing, and to keep the project within our budget. With our collective expertise, we overcame hyper-escalation and materials scarcity without asking for extra funds.
Read more:
- DJC: Innovation Hall breaks new ground in partnerships and processes
- Geekwire: University of Wash. Bothell and Cascadia College celebrate new STEM-focused Innovation Hall
- Everett Herald: New science, math facility opens in January at UW Bothell
- 425 Magazine: A Win for STEM Education in Bothell
- Puget Sound Business Journal: UW Bothell, Cascadia College unveil $79M Innovation Hall