Historically speaking, it’s no secret that construction hasn’t had the greenest track record in the world, and while the industry is making progress towards a more sustainable future, that progress can often seem frustratingly slow. As forward-looking ideas such as cross-laminated timber (CLT) or water reuse undergo rounds and rounds of testing to prove they fulfill the mandates of building codes around the world, it feels like a long wait.
But progress is happening! In Seattle, Lewis is involved in several projects with highly sustainable features, like CLT at UW’s Health Sciences Education Building and water reuse at 400 Westlake. We’re also taking a more proactive stance closer to home to make progress mile by mile.
Say hello to our new hybrid F-150 superintendent trucks.
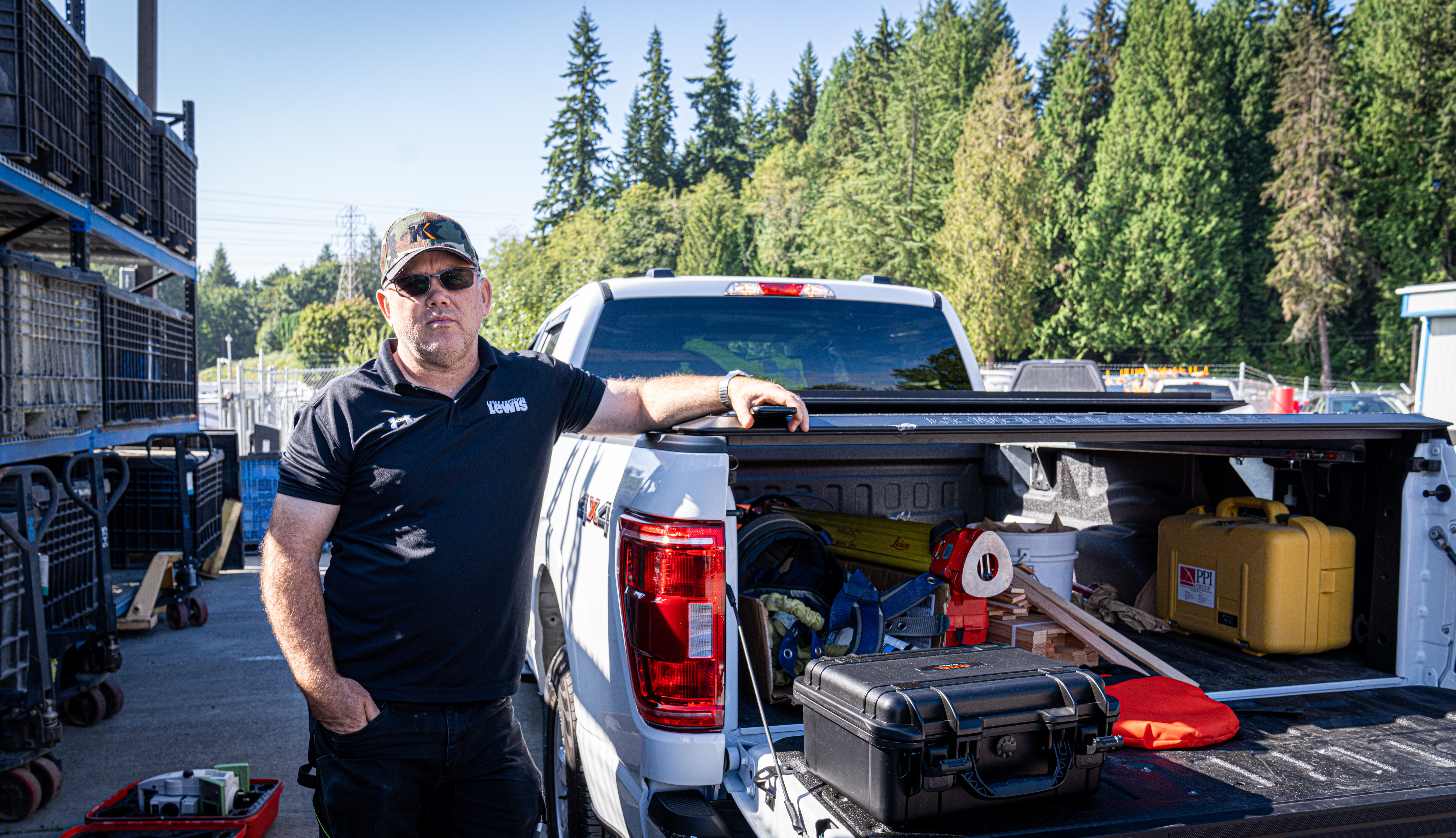
These new trucks are our first step towards electrifying our entire fleet of 39 trucks, with the goal of being fully electric by 2029.
We currently have two hybrid trucks in the fleet and are tracking mileage and performance closely to understand the real-world effects of transitioning our entire fleet. Right now, we’re seeing a miles-per-gallon increase from 15 to 21, which translates into 220 fewer gallons of gas per year, and a decrease of CO2 emissions from 7.3 to 5.3. And that’s just for one truck.
Expanded to the fleet, we could see a decrease of over 80 tons of CO2 per year or the equivalent of the energy use of nearly 10 typical homes!
One added benefit, we’re learning, is that truck users can keep their equipment charging overnight in the lockable bed. “I used to have to drag all my survey equipment into the house every night to charge it. Now I can just leave it plugged into the bed outlet and have a 100% charge in the morning,” say Aaron Stegmeier, Survey Forman and one of the recipients of the new truck.
Next year, we will also beta test the new F-150 Lightning, a fully electric truck. During this test, we will evaluate how we can charge fully electric trucks at a jobsite. Jobsites don’t always have the same infrastructure as your typical garage, and as most superintendents know, it’s not uncommon to have to park in a gravel lot or field far from any source of electricity.
To address this need, the Lewis Yard, which provides all equipment for our construction sites, is determining how we might be able to retrofit a typical jobsite to provide an electrical hookup for these trucks. What infrastructure do we need to provide? What changes to jobsite parking need to be made?
Once we roll out fully electric trucks for the entire 39-truck fleet, we could see improvements of 240 fewer tons of CO2 per year. That’s the same as taking 52 passenger cars off the road.
These two new trucks are just one step we’re taking to stay ahead of a new trend in the AEC industry. “We’re seeing more and more carbon footprint calculations of building materials in our projects,” says Tony Powter, Lewis Yard manager and the manager of our fleet. “Is the next step calculating the carbon footprint of equipment used to build the building? We want to be prepared for that.”
Another benefit of these trucks: A surprising amount of power (430 horsepower and 570lb-ft of torque), although not everyone’s using it to its full advantage. “The power? Oh yeah, I wouldn’t know. I drive like a grandma,” said Jim Rose, General Superintendent and long-time Lewis employee.